Introduction
HD Flexo is a new process for making digital flexographic (Flexo) plates. The improved plates are higher quality and print more consistently than standard digital Flexo plates. HD Flexo may be implemented without scrapping existing equipment and working methods.
With HD Flexo, the gap between Flexo and gravure and offset is closed. Bringing consistency, vibrant colors and increased print quality, HD Flexo raises the industry standard in Flexo printing. Flexo printing can now compete with offset for quality labels and with gravure printing for flexible packaging. And Full HD Flexo goes even further in the quality improvements.
Exceptional Flexo results start with exceptional Flexo printing plates. With Esko’s HD Flexo, not only are you able to deliver a new level of Flexo quality, you can also reduce the make-ready time on the press. What’s more, HD Flexo printing plates deliver greater run lengths. And because they need fewer washing cycles, the press is optimally used. There is a sustainable benefit as well. Printing flexible packaging on a Flexo press instead of gravure reduces energy use and CO2 emissions by as much as. Converters and brand owners can improve sustainability by taking advantage of the higher quality offered by HD Flexo.
How does it work?
HD Flexo by Esko combines 4000 dpi HD optics with unique print screening technologies to achieve sharper and more accurate imaging. The result is excellent print quality and a simplified plate production because the high-resolution optics deliver sharper imaging of text and lines and more clearly defined, better shaped screen dots.
High resolution imaging on the CDI creates a textured surface on the plate, improving ink lay-down and increasing ink density on the final print. The result is improved image richness and contrast. This is especially helpful for PANTONE colors, and for white under prints.
HD Flexo is able to create a textured surface on the Flexo plate or sleeve. This improves ink lay-down and increases ink density on the final print. This boosts image richness and contrast and is especially helpful for brand colors, and for white and spot color printing.
Full HD Flexo combines all the benefits of HD Flexo with a gravure-like ink lay down and a fully digitally controlled plate making workflow. Flexo offers now a level of quality and consistency with no need for compromises.
HD Flexo – 4000ppi Imaging Technology
- Increasing Image Screen Ruling has limits!
- Images are composed of 256 grey levels (Repro side)
- Number of natural grey levels = (PPI/LPI)²
PPI = CTP Imaging resolution LPI = job line count
(Natural grey levels are further reduced by dot gain compensation)
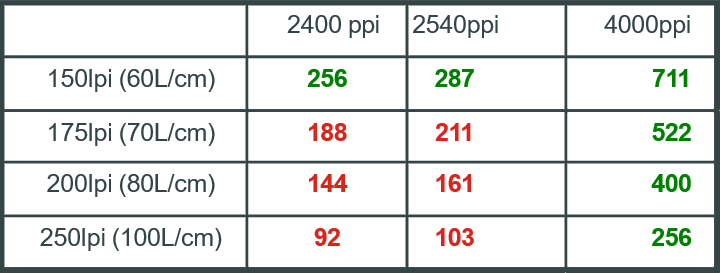
What exactly is High Definition Flexo?
HD Flexo is a unique imaging technology combining:
- High resolution imaging at 4.000ppi / 6µm laser spot size
- High Definition screening technology
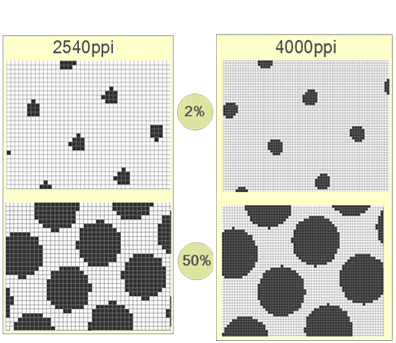
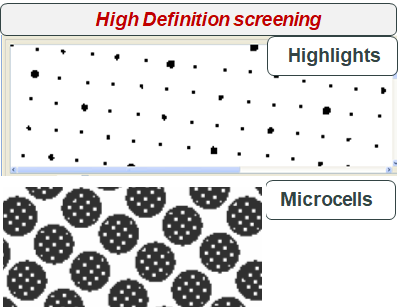
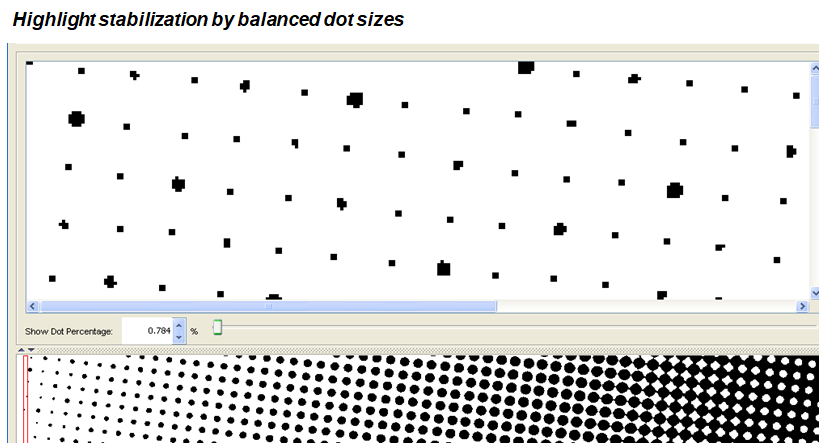
HD Flexo – Solids and Shadows

Ink laydown improved but still far from ideal
- too low solid ink density (SID) with fine Anilox rollers
- only marginally improvement with spot colors/white
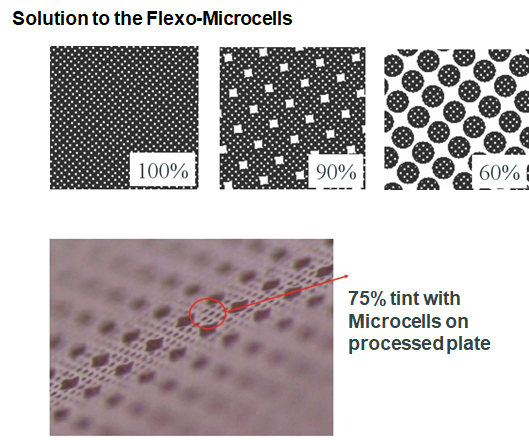
Full HD Flexo creates a unique dot shape
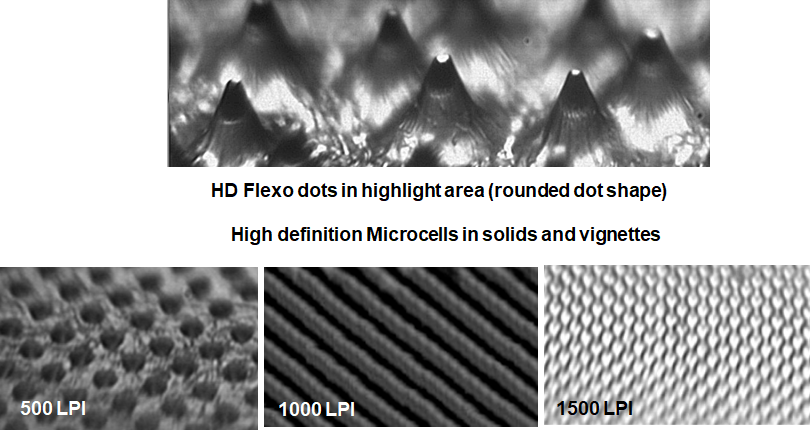
Full HD Flexo: Applications & Benefits
Full HD Flexo extends the boundaries of Flexo printing for flexible packaging. Depending on the screen ruling used, Full HD Flexo has different capabilities and benefits:
- Screen rulings between 110 – 130 ppi: Full HD Flexo improves the quality of solids and whites, print consistency, press speed, and job changeover. Existing presses and anilox rollers can be used.
- Screen rulings between 130 – 150 lpi: Full HD Flexo enables the conversion of gravure work to Flexo printing. Good image details and contrasts, highlights to zero and smooth vignettes can be achieved. Spot colors can be produced with higher vignette quality.
- Screen rulings between 150 – 250 lpi: the perfect solution to move gravure work to Flexo. The print quality is stellar: excellent details, brilliant colors and smooth transitions to zero.
Full HD Flexo in Flexible Packaging
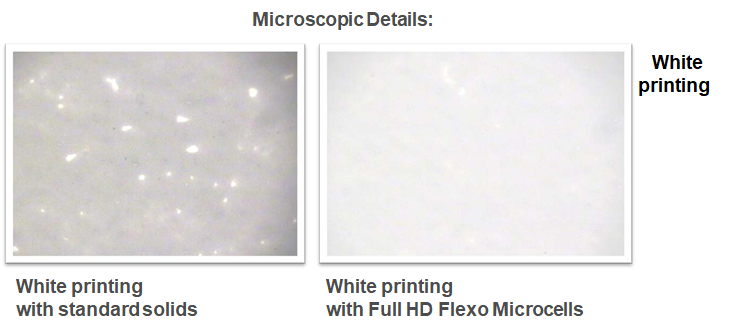
Benefits:
- Stronger white with same Anilox roller
- Saves a double press print units
- Same white strength with finer Anilox roller
- Reduces ink consumption (ca. –25%)
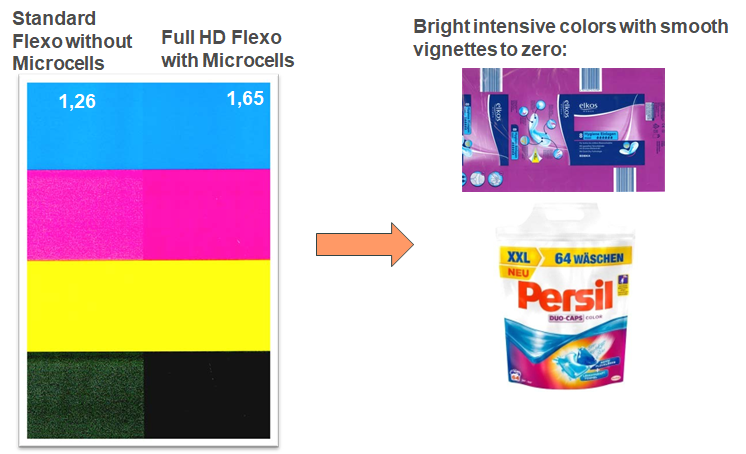
Full HD Flexo Print Quality
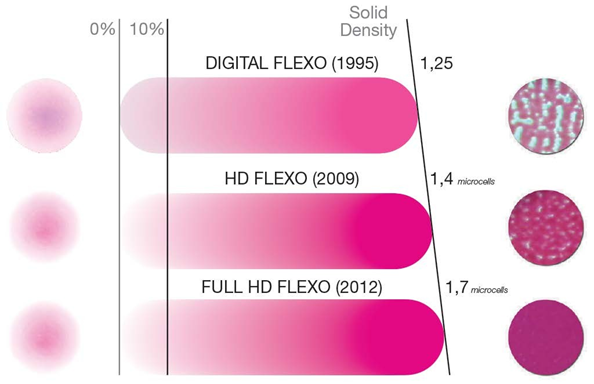
Full HD Flexo for Corrugated Post-Print
- Fluting reduction
- Process work becomes possible on cheap B-flute and even C-flute boards
- Improved image quality
- Improved highlight stability
- Better ink laydown
- Even with harder plates
- In some cases significant SID(solid ink density) increase (ink/substrate related)
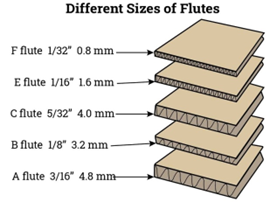
Full HD Flexo for Label Printing
- Better quality on gear driven presses therefore less gear marks
- Possible to use harder tapes. SID (solid ink density) increase
- Dots more foregiving against impression changes
- Identical printout of all Label repetitions
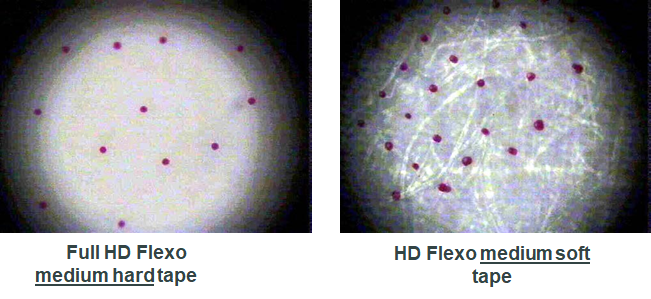
What is the CORRECT Solid Ink Density?
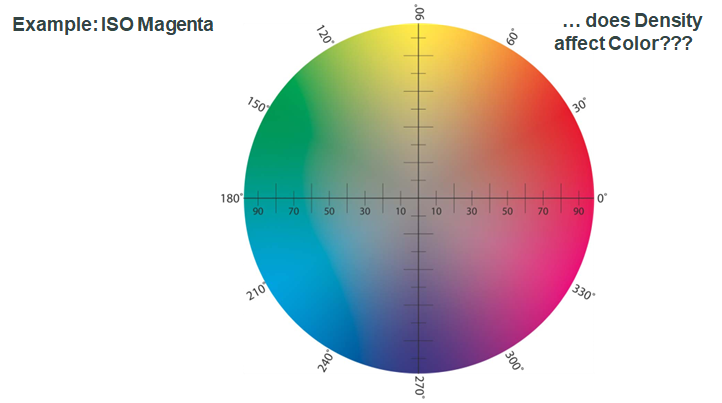
Spectral measurement at different solid ink densities:
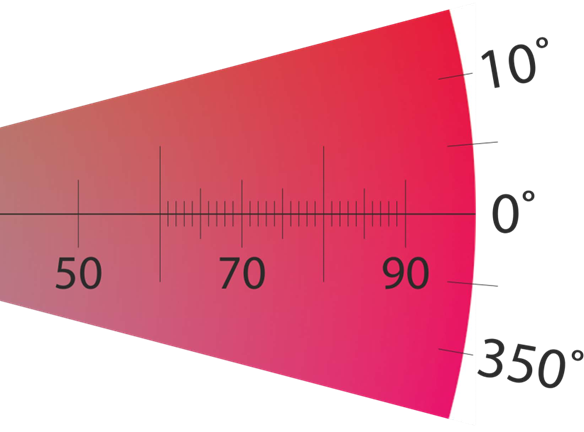
Select the right Full HD Flexo Solid Screening
- Optimal Ink Laydown (no pinholes) for CMYK, spot colors and white
- Select the desired ink density w/o changing the Anilox roller:
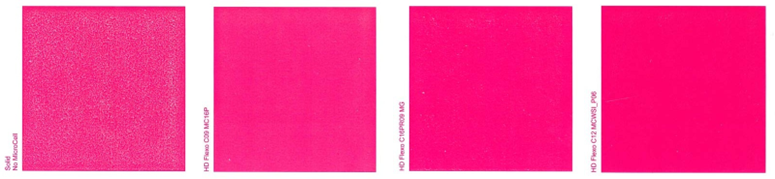
- üDifferentiate between spot colors, white and process colors:
- Process colors: Target SID between 1,4 and 1,5
- Spot colors: SID as high as you get….
- White printing: Opacity as high as you get…
About the author:
Mohammed Abdul Haleem
Email: packagingprinting@consultant.com
With about 29 years of experience in the Printing industry, he offers proactive recommendations, Flexographic Printing machine, Central Impression, Stack, or Narrow web, anilox roll specifications, flexographic printing sleeves, testing, inventory management, flexographic, Lamination Solventless, or solvent based, training, representation from experience in technical marketing,production,technical service, parts and supplies.
His experience covers the spectrum of flexographic markets including: pre-press, wide web flexible packaging , narrow web, tag & labels, foil, folding carton, corrugated packaging applications.