Introduction
The flexo presses becoming faster and more automated, the pressure for productivity improvements has been passed onto platemaking equipment manufacturers. The new flexo presses with faster changeover times going head to head with digital technologies in a race for short run jobs. The speed and efficiency of these presses meant growing pressure to reduce the restricted access in the platemaking process.
The challenge for plate manufacturers has always been to create a more environmentally friendly plate without losing the benefits and advantages of quality and efficiency. Water-washable plates were developed to meet that challenge and to help printers and converters approach their operations from a much more holistic perspective.
In addition to delivering excellent quality, these plates ensure a lower CO2 footprint in print production with a much higher press OEE (Overall Equipment Efficiency). Average improvement in OEE with water-washable plates is 33 percent. In flexographic printing, highlights can usually cause two potential problems. The first is the highlight breaking point, which prevents a vignette from printing smoothly to zero.
Photopolymer flexo plates usually start printing highlights at 5 percent to 8 percent due to dot gain, in the best cases. This means that gradations in vignettes suddenly break at that level, producing a visual contrast with the substrate; a visible breaking point or line well recognized as a print fault in the industry.This breaking point is virtually eliminated using water-wash technology due to its smaller dot size, low dot gain and high dot stability, especially when used in combination with the latest generation of screening technologies.
Significant Benefits:
HD Quality, no more solvents:
Compatible with both water- and solvent-based inks, Waterwashable plates enables quick production of ready to use plates, eliminates processing solvents and the corresponding disposal expenses and allows easy mounting and placing, while minimizing buildup and downtime spent cleaning the plate for printing.
Quick Production:
The first great benefit of waterwashable flexo plates is quick production: when a set of plates needs to be replaced urgently, a trade shop can save the client possible buildup downtime by producing water-based digital plates in 40 minutes, whereas, in the same time span, solvent-based plates would only be at the end of the washout step, Comparing the benefits are apparent: processing an Waterwashable plate (1.14 thickness) takes 8-10 minutes for exposure, 8-10 minutes for washing, 10 minutes for drying. Which means the plate is ready for printing within 40 minutes… set against the over 2 hours needed by solvent-based photopolymer plates!
Color density like Rotogravure:
However, it is possible to obtain colour density comparable to rotogravure with no need to produce multiple plates for the same work, thus making pre-printing work quicker and easier. Most importantly: many of the problems that are commonly encountered in printing with extreme screens do not arise when using Waterwashable plates. Solvent-based plates usually produce faded images and can lead to dot gain in high lights. In many competitors’ plates printed dots of 1% manifest results between 7 and 11% and can suffer, resulting in unclean printing in halftones. On the other hand, waterwashable plates has excellent colour density, which means sharper nuances, and to this day 1% dot gain is between 3 and 5% in flexible packaging.
Extra Long runs, maintaining with all type of Inks:
Another advantage recognized by various printers is that with waterwashable plates no longer have to adjust pressures. The plates last much longer, do not swell and allow extra long runs, while being suitable for all types of ink: water-based, solvent-based and UV.
In a nutshell the benefits are:
- Quick production (40 minutes for a plate that is immediately ready to use!)
- Colour density comparable to rotogravure: sharper nuances. 1% dot gain is between 3 and 5% for flexible packaging
- Elastic mounting and easy placing
- Excellent ink transfer and fewer buildup downtime spent cleaning the plate.
- Compatible with any type of ink: solvent-based, water-based or UV.
- No bump. Stable plate. Extra long runs.
- Elimination of solvents and related costs.
Equipment for Processing water-washable plates
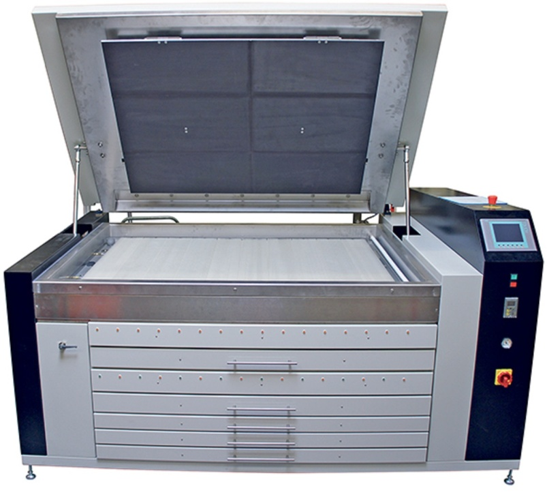
All-in-one clamshell unit
- Washout section: the plate is fixed face down on the plate holder. Relief washout is obtained by orbital movement of the plate over a brush frame. Automatic closing and opening of the brush frame at the end of the cycle.
- Exposure: Pull out vacuum drawer with draw down sheet to hold plate during UVA exposure.
- Light finisher & Px: Pull out drawer for UVC anti-tack exposure and UVA combined for post exposing the plate
- Dryer: Three dryer drawers with temperature control and exhaust blower.
- All configuration possible: WO / WO-D /…
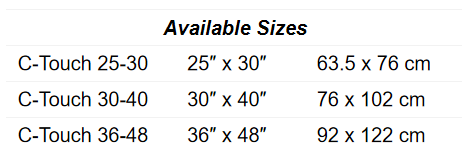
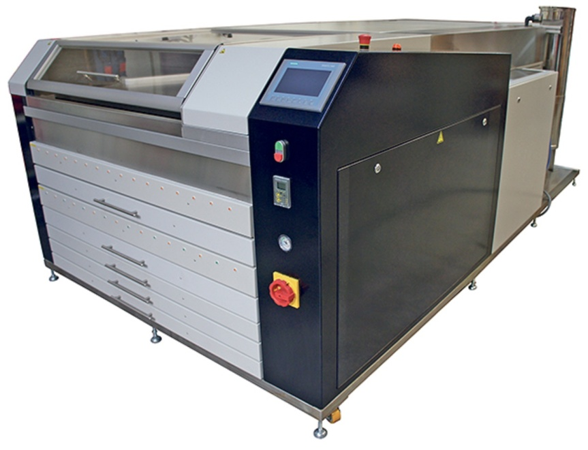
Continuous Flow-Line unit
- The System series washout section includes automatic rinsing and pre-drying to reduce plate handling time.
- The plate is mounted on the sticky plate and excellent relief washout is achieved by the orbital movement of brush heads with the plate moving back and forward. This result in clean dot reproduction, also for HD flexo.
- Exposure: Pull out vacuum drawer with draw down sheet to hold plate during UVA exposure.
- Light finisher & Px: Pull out drawer for UVC anti-tack exposure and UVA combined for post exposing the plate
- Dryer: Three dryer drawers with temperature control and exhaust blower.
- All configuration possible: WO / WO-D /…
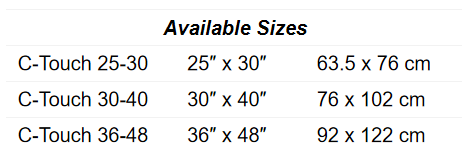
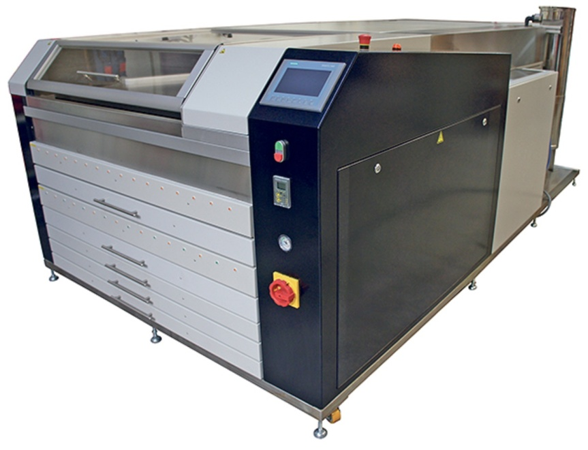
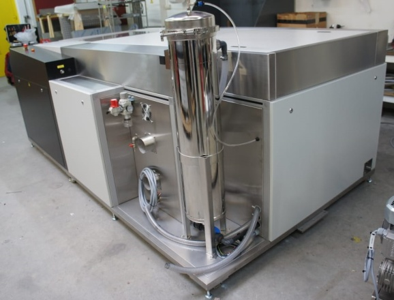
Continuous Flow-Line unit
Model : S928B Internal Combination
- In the S928B, the washout section is internal to provide a very clean work area and simplified plate handling.
- The plate mounts on a plate holder where relief washout is obtained by the orbital movement of the brush heads under the brush frame.
- This all-in-one design has a small foot printand eliminates the need for large space requirements. It includes pull out drawers for exposures (including HD), light finishing, and three dryer drawers with temperature control.
- It will deliver approximately three plates per hour up to 36” x 48”, 92 x 122 cm format
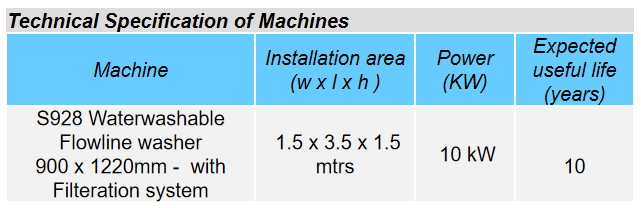
Plate-Making Process
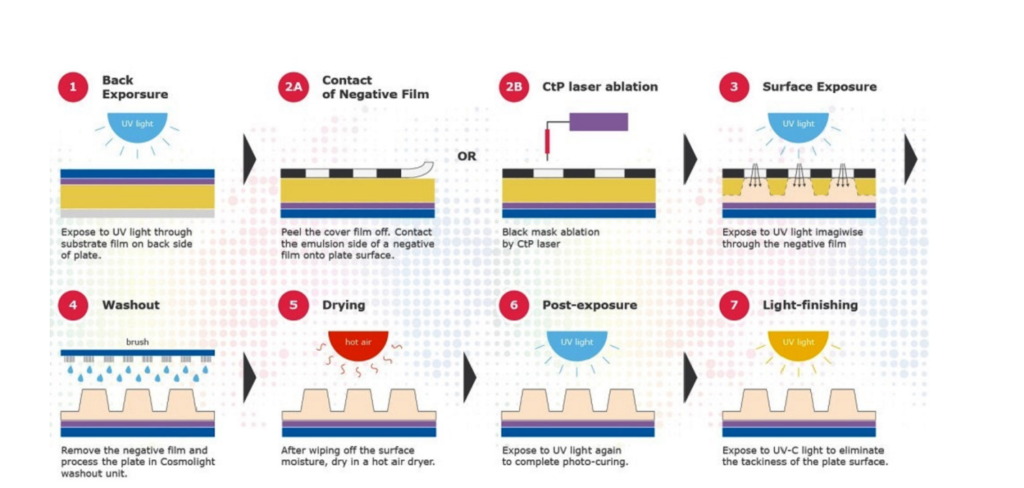
Comparison of Plate making parameters:
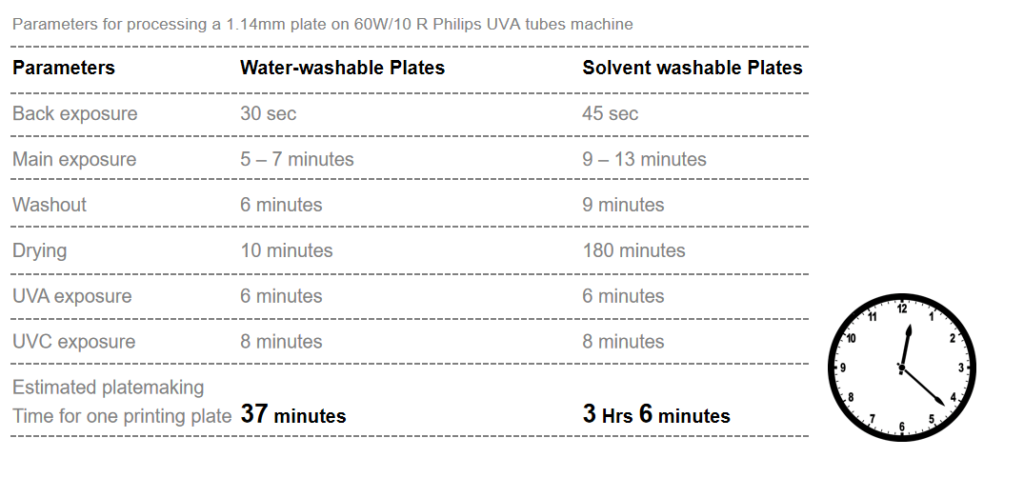
Comparison of Plate making time for water-washout plate:
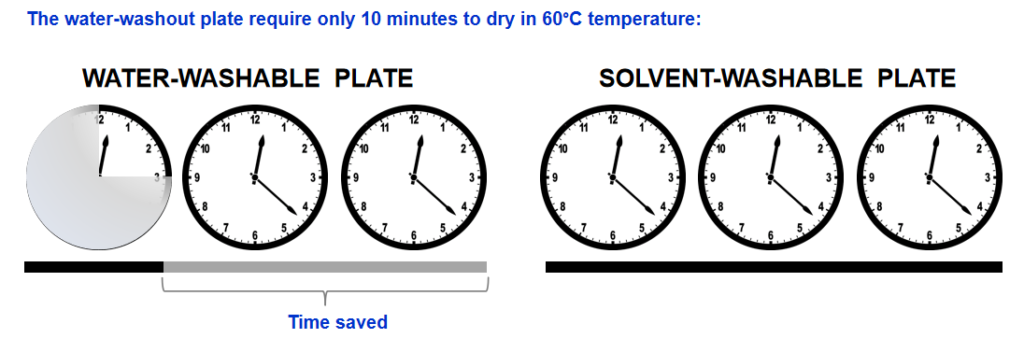
About the Author:
Mohammed Abdul Haleem
Email: packagingprinting@consultant.com
With almost 27 years of experience in the printing industry, he offers proactive recommendations on anilox roll specifications, flexographic printing sleeves, testing, inventory management, flexographic equipment applications, training, representation from experience in technical sales, marketing, production, technical service, parts, and supplies. His experience covers the spectrum of flexographic markets including wide web flexible packaging, narrow web, tag & labels, foil, folding carton, corrugated packaging applications.