INTRODUCTION:
Flexo plates are a critical component of the printing system. Printing is a system—viewing plate making in isolation doesn’t address the total print process. A system has multiple components that interact with each other and influence the performance of each. Great plates with the wrong anilox rolls offer nothing to improve quality.
Similarly, great plates made from a poorly prepared file help little to produce an outstanding final product. So, looking upstream and down stream is necessary to ensure your plates are supporting the total printing system.
Superior printing plate:
- Have sufficient resolution for the graphics to be reproduced on the substrate for the job (paper, film, foil, etc).
- Are produced to optimize press and ink performance.
- Are made in a controlled and repeatable manner.
Let’s look at several important factors in making great plates.
Dot Formation
The accuracy of the dot and the formation of the minimum dot is inspected with a microscope (100X)
Specific characteristics are evaluated and verified to confirm a successful minimum dot; this method ensures that, although the minimum dot is small, it can be used as an effective control point. This may or may not be the dot percentage used in the production job
Peak 2034 Wide Stand Microscope – 100 X
Peak Wide Stand Microscope is a simple measuring microscope designed to be compact and light weight, but characterized by a wider field of view than that of the conventional microscope. It allows not only to provide magnified view of fine pattern and contour of objects, but also to measure length and compare dimension by using a scale included in the eye-piece. Has a helicoid focus mechanism.
Peak Wide Stand Microscope will be useful not only for the general observation but also for improving accuracy in precision machining and securing uniform quality in the inspection process
The caliper of the plate is one of the most important factors when controlling the impression setting on the press machine; any low spot will not print or will cause overprinting for the remainder of the printing plate. All areas must be at full print height including solids and halftones.
The relief specifications must be defined and confirmed depending on the caliper, the graphic details, press machine requirements, and other variables. Target relief specifications should be confirmed with the printer.
Thickness Gauge JD-200-25
- Measuring range 0 – 25 mm / 0 – 1 inch
- Resolution 0.01 mm / 0.001 inch
- Self-closing thickness gauge with high accuracy and resolution
- Thickness gauge JD-200-25 features an easy to read digital display along with the high accuracy
- The thickness gauge is available with 5 different feelers, which can be found below
- Measuring by spring force 1.9 N
- Opening by lifting device (lever) – self-closing thickness gauge JD-200-25
Plate hardness
It is an another important factor when selecting plate material. The unit of measure for hardness is Shore A, measured with a durometer. Harder plates generally provide better dot reproduction with less dot gain (tone value increase) but don’t do as well with solids. Similarly, hard plates do well on very smooth substrates but struggle with rough surfaces.
Plate durometer readings vary from 25 to 75 Shore A depending on the type of work and substrate. Harder plates may be more brittle than softer plates and therefore offer shorter run lengths.
Shore Durometer – HPSA
Durometer according to Shore for determining the surface hardness of soft rubber, Photopolymer Plates, elastomers, natural rubber, soft PVC, leather, etc. Shore A hardness tester according to DIN 53505, ISO 7619, ISO 868, and ASTM D 2240
- The spring-loaded outer ring assures a constant measuring pressure and eliminates false readings due to the difference between operators
- Flat bottom prevents tilting and improves the measuring accuracy
- Working face 18 mm Ø
- Adjustable Min./Max. indicator marks to highlight the working range of the hardness tester
Focus & Stain Test
Interval: Minimum 1x per week & when Visual Inspection fails
Tools: Transmission Densitometer
Transmission Densitometer
A film transmission densitometer and a high-precision illuminated magnifying glass for the visual control of printing results.
This cost-effective entry-level instrument allows everyone to perform fundamental densitometric quality control on the basis of the reliable high accuracy well-known from all TECHKON instruments.
The DENS indicates densities, dot area, and gray balance clearly legible on a large color display. Automatic color and gray balance detection speed up the measuring. In addition, the device is easily operated by only three buttons. The whole measurement is provided in a split of a second.
Spectro-Densitometer
SpectroDens is your all-purpose, modern measurement device for every application from pre-press to print. Whether it be in pre-print for verifying proofs, for ongoing quality control at the printing press, during delivery inspection of paper and print products or in a color lab, SpectroDens is exceptionally suitable, no matter which application.
It combines the qualities of a highly accurate spectophotometer and an easy-to-use densitometer. Measurement is spectral, i.e. the entire color information – the spectral fingerprint of the color – is precisely registered.
The data is converted into measurement data for descriptive analysis and display.
The device works strictly according to the standards valid for the Graphic Industry. It is particularly good at evaluating the Ugra/FOGRA-media wedge because it toggles between colorimetric measurement without polarization filter and density measurement with filter at the push of a button.
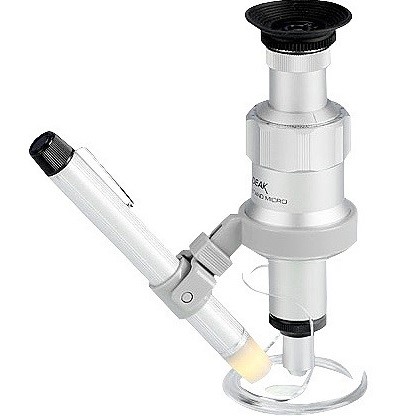
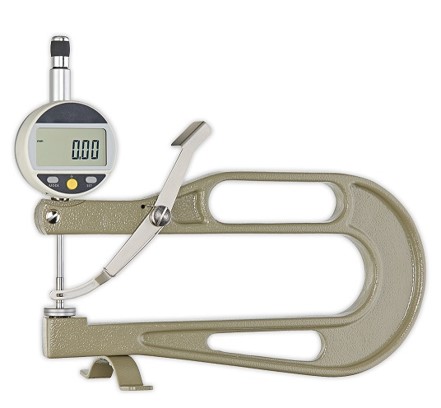
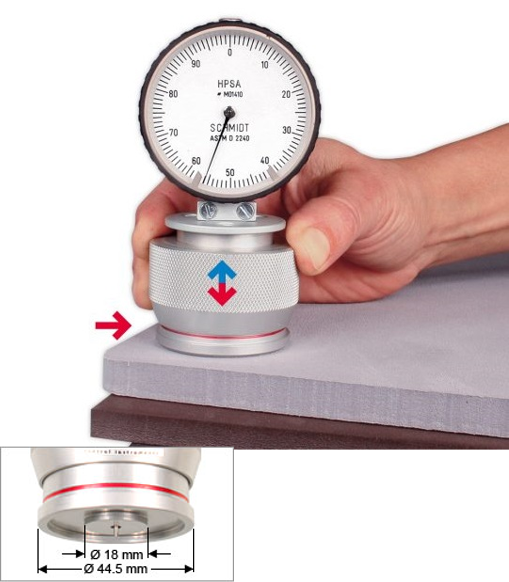
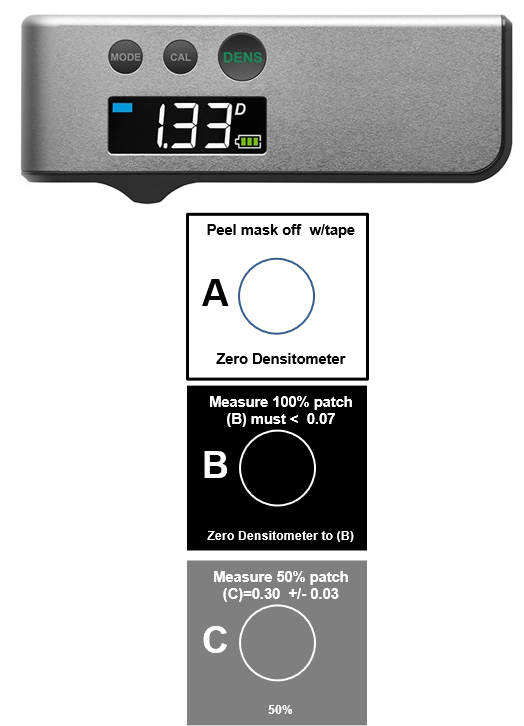
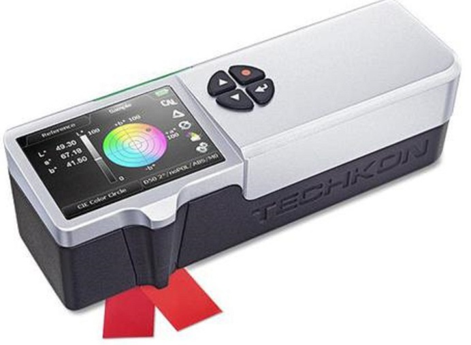
UV output check
Measure 9-points across the bed
Interval: 1x per week
Tools: UV-A Meter
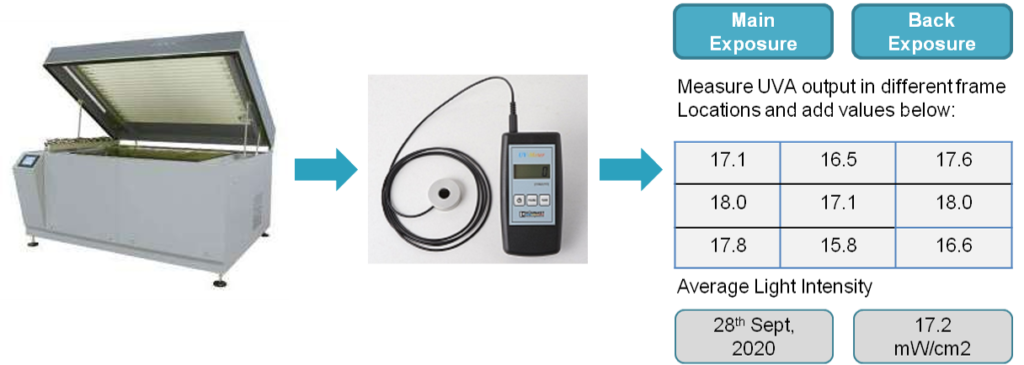
Betaflex PRO Flexo System Analyzer for
HD FLEXO & MORE!
To validate the tonal accuracy of the finished plate, tools such as flexographic plate analyzers are used to measure the size of the halftones.
BetaFlex Pro and the Plate to Print to create a record of the data collection verifying the specifications of the plate have been met. In any case, whatever the device used, calibration procedures and the process of taking measurements must be clearly documented along with the approval/rejection criteria.
The Problem: Process variability, uncertain results, wasted material
The Solution: The Betaflex PRO system simplifies process control with a familiar interface, unparalleled accuracy, and a powerful toolbox of functions.
The Benefits: Detect process variation before expensive errors propagate through the system. Automatic data collection, plotting, and statistical analysis keeps the operator informed and the process on target.
The new Betaflex Pro system operates at the highest resolution to provide the most accurate and consistent measurements. HD Flexo, stochastic screening, and all the most sophisticated prepress techniques can be measured and controlled with ease and accuracy.
Hand-Held Refractometer
A refractometer is a small piece of equipment commonly used to check the sugar density (in percent Brix) for fruit harvests. It is often used in the quality control of jams, syrups, and almost any liquid where the sugar content is critical.
Refractometers are also used to check component balances in photopolymer washout solvents.
Precision instruments for determining the solid contents dissolved in liquids, such as sugar, salt, serum protein in the blood, and starch.
Dissolved solids can be determined in seconds. The hand-held refractometers fit in every pocket! Delivered in a handy storage case with conversion tables.
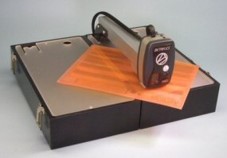
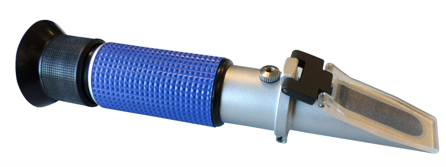
Summary:
Platemaking is a critical part of the printing system. It can be controllable and predictable with some standard best practices. Spend time analyzing, measuring, and improving your plate processes and you will be on your way to better printing. Your press room will love the results.
About the Author :
Mohammed Abdul Haleem
Email: packagingprinting@consultant.com
With almost 27 years of experience in the Printing Industry, he offers proactive recommendations on anilox roll specifications, testing, inventory management, flexographic equipment applications, training, drawing from experience in technical sales, marketing, production, technical service, parts, and supplies. His experience covers the spectrum of flexographic markets including wide web film, narrow web, tag & labels, foil, folding carton, corrugated packaging applications.