Right Doctor Blade for Flexographic Printing
Introduction:
The core purpose of a doctor blade in the flexo process is to remove excess ink from the anilox surface; to leave behind a perfectly smooth ink film for transfer to the image on the plate and to do this without damaging the anilox.
The most precise and even metering takes place when the blade makes contact with the anilox in the reverse or sheering position at an angle between 30° – 35°.
There are only three basic types of doctor blade:
- Metal (steel, stainless, and thermal coated, i.e. ceramic and carbide metal blades)
- Plastic (polyethylene)
- Composites (laminated resin structures which include a binding material)
Blade Edge Profiles
Lamella doctor blade
The lamella edge ensures that the thickness of the edge remains unchanged. Within the lifespan of
blades, doctor blades with a lamella edge can perfectly and quickly make contact with the cylinder
roller the moment the printing press begins operation. The doctor blade with lamella edge minimizes waste.
The edge of the common, middle-end, and high-end coating doctor blades is standard.
Carbon steel doctor blade with lamella edge: The blade is made of carbon steel and coated with a special coating that minimizes the wear of the doctor blade resulting from pigment particles, which prevents the appearance of ink streaks and the change of print color. Our common coating doctor blade can be used in the coating process.
Special coating doctor blade
The hardness material coating of the blade edge extends the lifespan of the blade, reducing the change time of the doctor blade, protecting the cladding of the anilox roll and pattern. Besides, middle end and high-end coating doctor blades effectively remove excess ink better and prevent the appearance of ink streaks. The special coating doctor blade can even be used to remove excess UV ink.
Beveled doctor blade
Doctor blades with a beveled edge with a bevel angle from 4 to 15 degrees have great elasticity and maintain blade contact with the cylinder at a suitable angle. Beveled edges with larger angles can reduce the wear of the blade and break the frequency of the blade. The smaller the contact area, the better effectiveness in removing ink. So beveled doctor blades with higher hardness and better durability are more popular.
Doctor blade with rounded edge
The doctor blade with a rounded edge is classified by the radius. The blade with a large radius is usually
used to print large-area patterns on textile. And the blade with a small radius is usually used to print
products with low accuracy by using ink with low viscidity.
Doctor blade with 3-degree bevel edge
The edge with 3-degree angles ensures the stability of the doctor blade, minimizing the bending of the blade under excessive blade pressure and hazing.
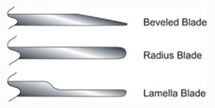
Blade Thickness
Thickness considerations:
- Blade Material dependant
Plastics & Composites thicker than metals
- Application dependant
- Corrosive ink or coating or environment.
- Ink pigmentations or material (ex. TiO² white)
- Metering or Containment
- Anilox Geometry
- 30 & 60°
- 45° Quad
- Channeled
- Trihelical
- Anilox Screen
- Process & solids
- Coatings and adhesives
Doctor Blade Material Selection
Carbon Steel: Either blue or white carbon steel blades are common and mostly vary in cosmetics. High quality carbon steel is strong, allowing you run a thinner blade successfully. Do not try to save money on cheap blades if you are using steel.
Stainless Steel: An alternative when corrosion is an issue. These are softer than carbon steel and will tend to wear faster on ceramic anilox rolls.
Plastic Blades, UHMW: These have become popular due to some improvements in wear – they are unaffected by corrosion and safer in use. Typically used in corrugated applications, they tend to be thicker and work as effectively as steel blades for doctoring. Plastic works great for a containment blade in a chambered system.
Composite Blades: One of the most promising and evolving innovations in the anilox and doctor blade relationship. Technology has allowed thinner blades with improved spring strength and structure to operate in the most challenging press room environments. The benefits include: long wear life, being unaffected by corrosion.
Refining Print Consitency and Blade + Anilox Life
- Proper setup of blade
- Correct blade holder and Foam End seal
- Correct blade to anilox LPI and volume
- The accurate blade type to ink
- Lightest possible blade pressure
- Good Printing Machine maintenance
- Clean and filtered ink
- Optimum viscosity inks for job
The blades should fit tight without leaving waves and the ink film should be chosen only by the roll so that there is no excessive ink.
Problems in Flexographic Printing
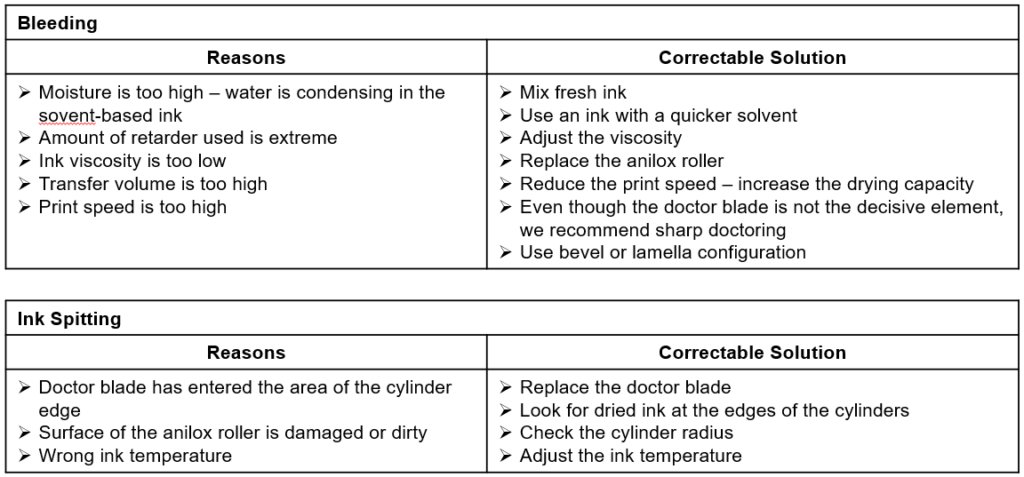
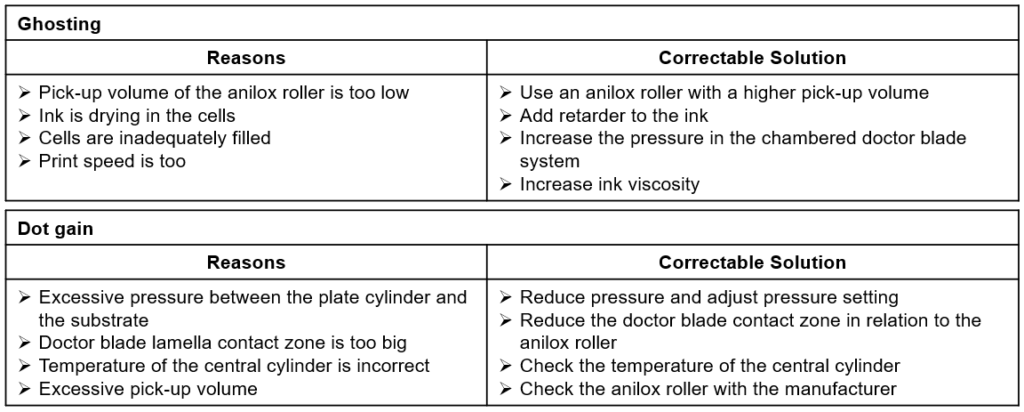
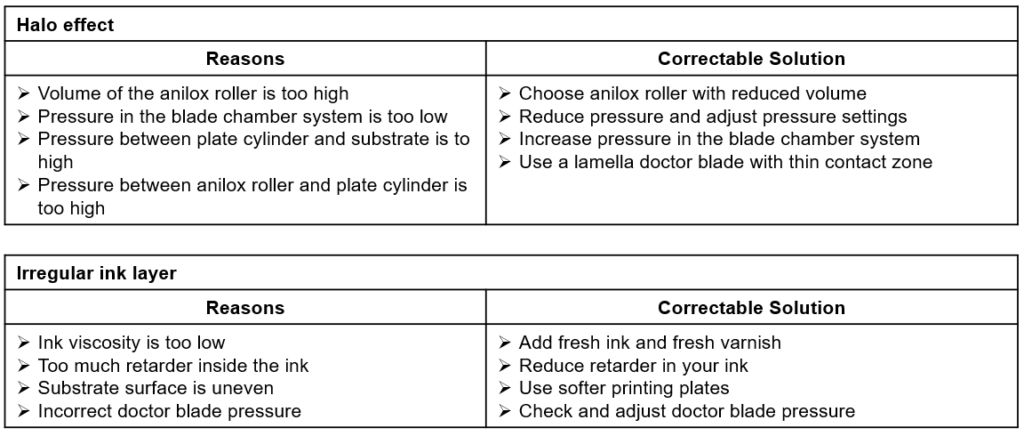
About the Author:
Mohammed Abdul Haleem
Email: packagingprinting@consultant.com
With almost 27 years of experience in the printing industry, he offers proactive recommendations on anilox roll specifications, flexographic printing sleeves, testing, inventory management, flexographic equipment applications, training, representation from experience in technical sales, marketing, production, technical service, parts, and supplies. His experience covers the spectrum of flexographic markets including wide web flexible packaging, narrow web, tag & labels, foil, folding carton, corrugated packaging applications.